Article: Infrastructure Monitoring
Continuous Track Monitoring CTM2.0
DB ST has developed a product that can be deployed onto any passenger service rolling stock, thereby eliminating the need for bespoke infrastructure monitoring vehicles. Importantly this system requires almost no maintenance and hence little reliance on the operator or maintainer to ensure that the equipment is operational. CTM2.0 monitors the infrastructure during normal passenger operations, collects data relating to the condition of the rail head, transmitting this information via cellular or Wi-Fi networks to a central server, for interpretation. This allows track defects to be identified and monitored, enabling action to be taken in a preventative manner before defects can develop and issues occur.
Continuous Track Monitoring

DB ESG received a contract from Network Rail to deliver the DB Systemtechnik Continuous Track Monitoring product (CTM2.0) for a operational trial in the UK during 2021/22. This project is part of the wider In Service Monitoring trial being led by Network Rail’s Research & Development team, looking at a number of train-borne track measurement/monitoring systems on in-service vehicles. In total, eight supplier solutions were selected to run trials.
This trial has enabled Network Rail to assess the suitability of DB’s system in helping them to reduce the number and impact of service affecting failures, including predicting future condition to enable preventative maintenance actions to be implemented.
For this project, DB Systemtechnik (DB ST) provided the CTM2.0 equipment on a loan basis. They then monitored remotely, for the 6 month duration of the trial, analysing the data and supplying Network Rail with regular reports detailing the actual track condition and predicting future track conditions.
DB ESG was responsible for the vehicle design modifications required, all necessary approvals, material supply, installation of the CTM equipment, and testing and commissioning of the system.
DB ST‘s CTM2.0 equipment was installed onto a Mark 3 driving van trailer (DVT), which was operated in normal passenger service by Chiltern Railways, on the Birmingham to London Marylebone mainline.
The minimal CTM2.0 equipment consisted of external vehicle mounted sensors and an antenna, connected to an equipment enclosure inside the vehicle. The sensors measured the longitudinal level, track twist, dynamic alignment, ride comfort, cyclic top, speed and the vehicle’s motion response. The antenna transmitted the data to a land-based computer platform, which received, stored, processed and reported on the data.
Overhead Line Monitoring
DB ST offers high quality Overhead Equipment Measurement Systems (OHE) that monitor the overhead lines. These products can be used for acceptance tests for new pantographs or overhead line equipment or to monitor existing lines, helping to avoid accidents, damage to infrastructure or network issues through the early detection of catenary issues. These products can be added onto normal passenger service vehicles to enable proactive maintenance planning.
Overhead Line Monitoring Reference
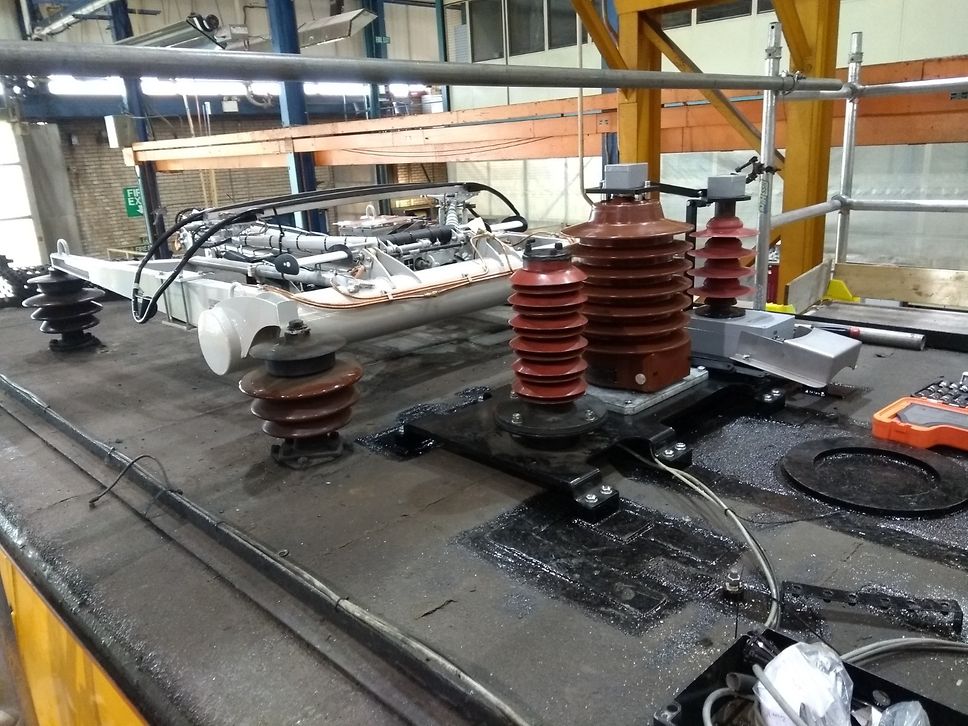
In November 2018, DB ESG received a contract from Network Rail to provide DB Systemtechnik’s proven overhead line monitoring equipment to enhance Network Rail’s existing infrastructure monitoring fleet.
Initially, the focus was to deploy two monitoring systems onto Network Rail’s Mobile Electrical Network Testing, Observation and Recording (Mentor) Test Coach. The overhead line monitoring system fitted to Mentor is now working as promised and is being regularly used by Network Rail to commission new overhead lines and detect any issues.
DB ESG has also installed a single system onto a Class 390 Pendolino unit to cover a specific area of the network. This system will be providing data daily, via normal passenger train service operation. The regular collection and assessment of asset condition data will support Network Rail’s ambition to move towards a ‘predict & prevent’ maintenance approach.
In October 2020, DB ESG was awarded a further contract from Network Rail to provide technical support for the Mentor and Class 390 Pendolino overhead line monitoring systems. This additional order is for the provision of support for eight years. This contract marks a significant shift in DB ESG’s offerings to the market, supplying services beyond its normal standard warranty period provision.
Crossing optimization tools ESAH and Scorpion
The following tools, ESAH & Scorpion, can be combined to provide a comprehensive design and analysis capability, enabling crossing design optimisation by understanding in detail the relationship between loading and crossing shape. This provides significant opportunities for life and reliability enhancements.
ESAH-Mobile
DB Systemtechnik’s technical team have developed an efficient & cost-effective diagnostic system for monitoring & assessing the condition of rails & switches, known as ESAH (Electronic System Analysis Crossing). ESAH uses a multi-axle sensor to determine the condition of railway points. It does this by measuring the actual accelerations (impact) encountered by the crossing as a vehicle passes through the section.
Wear on switches, and hence their life and reliability is influenced by a number of factors, but primarily these are material, design, track layout, track substructure / superstructure and the vehicles that pass over it.
ESAH-Mobile detects, for each wheelset, whether a normal overrun, a striking of the flange against the rail head on the crossing (positive) or on the wing rail (negative) has occurred, allowing the wheel guidance in the track channel to be assessed. Knowing this enables the identification of potential improvements either on the entire component or the wheel / rail interface. For instance design optimisation can be undertaken that includes consideration of overall design & material selection, along with track & transition geometries.
The benefits of utilising ESAH and performing the optimisation analysis manifest themselves in different ways. As an example, selecting an improved material will lead to an initial increase in component cost, but this is significantly outweighed by the gains. For instance, in operational service life and reliability, which also have the consequence of lower maintenance cost and less network outages (i.e. performance improvements).
The data can either be saved to the device or transmitted for later analysis in the cloud.
Scorpion
Scorpion scans the crossing components and measures the 3D geometry, to give an accurate and detailed measurement of the rail and turnout profiles.
Scorpion consists of:
- a frame providing a rigid datum base
- an integral drive system, laser measurement head and control unit
The Scorpion measurement head automatically transitions over the profiles being inspected, capturing the profile of the rail /welding / switch / turnout. The device control unit has a keyboard and LCD display. Measurement results are saved in the internal memory of the device for later transfer to laptop or tablet. The measurement result is the 3D model of the measured object, which is an exact representation in both the lateral and transverse direction.
Using the analysis software enables:
- merging of multiple measurements into one object
- generating of the arbitrarily selected 2D profiles in a 3D body-model with a load and wear calculator
- calculation of the longitudinal profiles / ramps for a comparison to other wear-states
- generating measurement reports
The system can provide the user with any transverse section profile with an accuracy greater than 0.03mm. The results can be used for mechanical contact calculations or in the design department by switch manufacturing companies.
The software makes it possible to recognize the particular crossing elements, i.e. vee, left and right wing rails. Based on these elements, the mathematical point of the crossing is calculated. To determine the longitudinal wear of the measured elements the user can define a section, along which the software will calculate the measured shape (centre / or running line). In this way it is possible to determine crossing point wear in the vertical and / or horizontal direction.