Article: AM production of obsolete toilet flap
(Derby, October 2021)
Overview
DB ESG is working in collaboration with the rolling stock leasing company Angel Trains on projects that incorporate 3D printing solutions (also known as additive manufacturing or AM) to address UK rail industry challenges, in particular the issue of obsolete parts. AM has the added potential to lower costs for train operating companies, as smaller volumes of parts can now be produced cost-effectively, rather than in mass quantities. It was also found to be a way to address supplier issues during the Covid-19 pandemic, as parts could be produced quickly and safely, whilst following lockdown guidelines.
The train operator, Great Western Railways had an issue with toilet flap assemblies on six of the Microphor Spacesaver toilets on their Class 165 units. The toilet flap assembly plays a key role in the toilet flushing process, being the part that lets water flow out the tank into the bowl when flushed.
These 6 toilets could therefore not be used without correctly functioning flap assemblies. The original part was obsolete and the toilets were due to be replaced just six months later. The train operator required a cost-effective solution quickly to enable the toilets to be usable over the remaining time period.
DB ESG scanned the component parts, completed an engineering assessment, validated suitability for production using AM. A prototype was then printed to enable the operator to check fit and form. Following the successful trial fit a small batch of production parts was delivered directly to the depot.

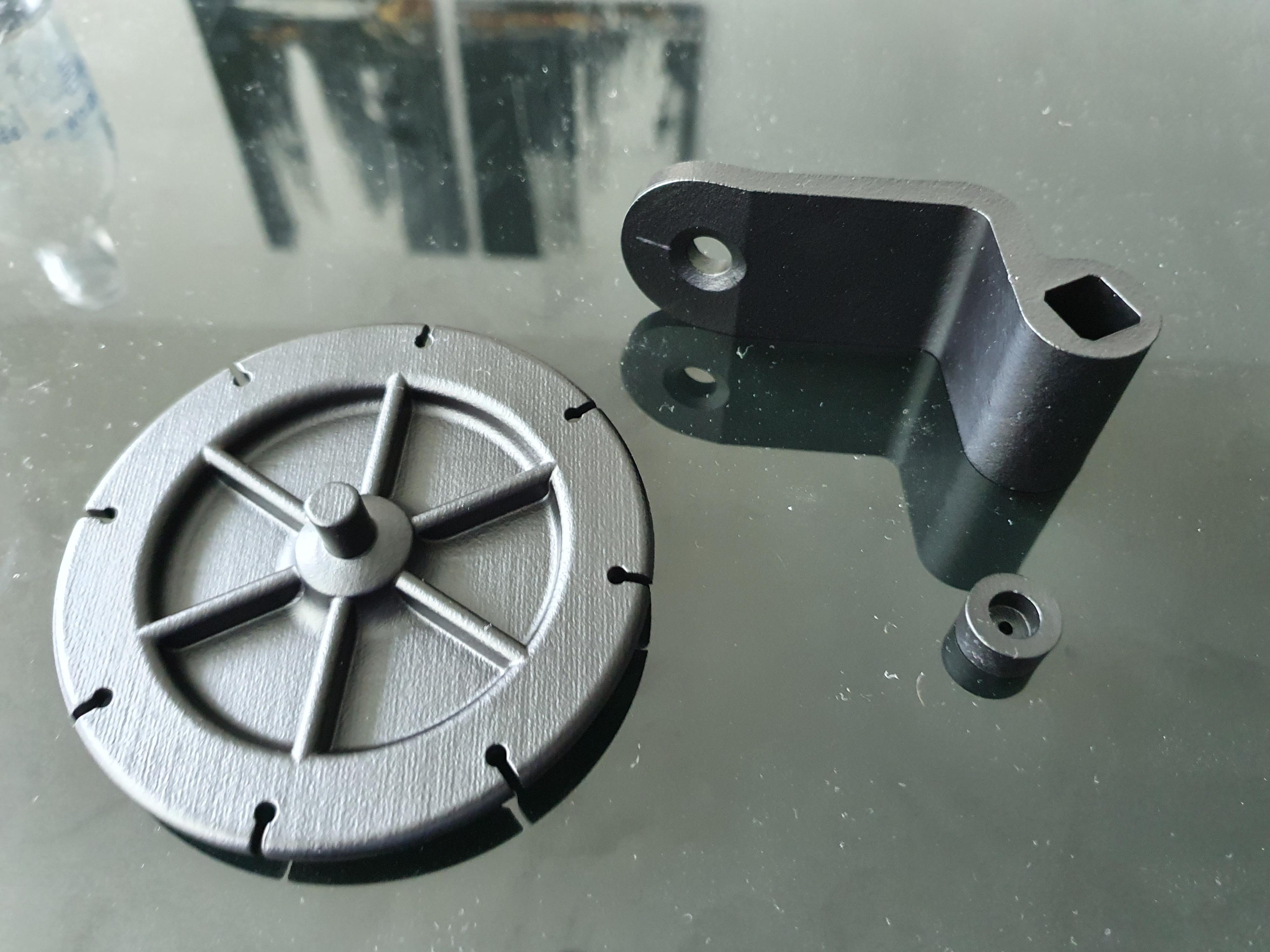
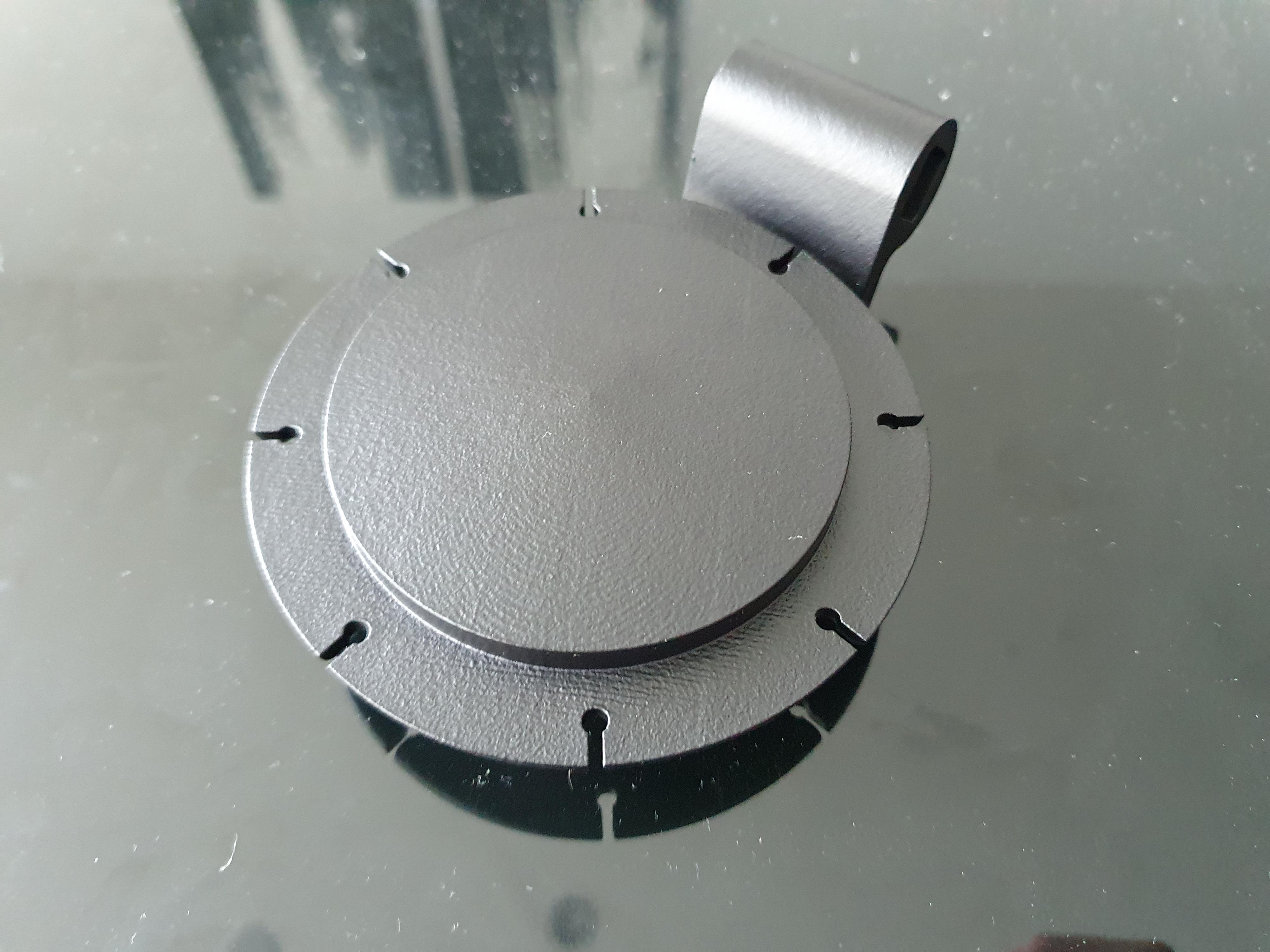
Work Undertaken:
- The current toilet flap was 3D scanned at depot and it was reverse engineered.
- The scan was converted into a 3D CAD model.
- DB ESG decided to produce the assembly with its original design unchanged, thereby maintaining the three-piece construction (a disc shaped flap with pin, an arm and a retaining cap). A proof of concept was printed using FFF technology in PETG.
- The three parts were 3D manufactured using MJF PA12.
- The parts were then AMT chemically smoothed, as the part needed to be located within the toilet bowl and therefore waterlogging and part degradation needed to be avoided.
- The sections were then adhesively bonded together to create the final functional item.