Article: AT300 Battery System - Design Project for Hitachi Rail
(Derby, 29. August 2022)
Overview
In March 2021, Hitachi Rail Ltd. contracted DB ESG to undertake a concept development exercise that considered the feasibility of producing a battery raft to house five tonnes of battery modules. This battery raft was to be attached to the underframes of the AT300 vehicles in place of the original generator, with a new cooling system fitted to the vehicle roof. Each battery raft was to originally house 18 independent battery units (BU), together with a box to house switches and electrical controllers. Every BU was to also be enclosed within its own fireproof pocket and connected to a coolant circuit, with each containing its own closed-circuit force air cooling system, using the supplied coolant to cool the air within the battery unit.
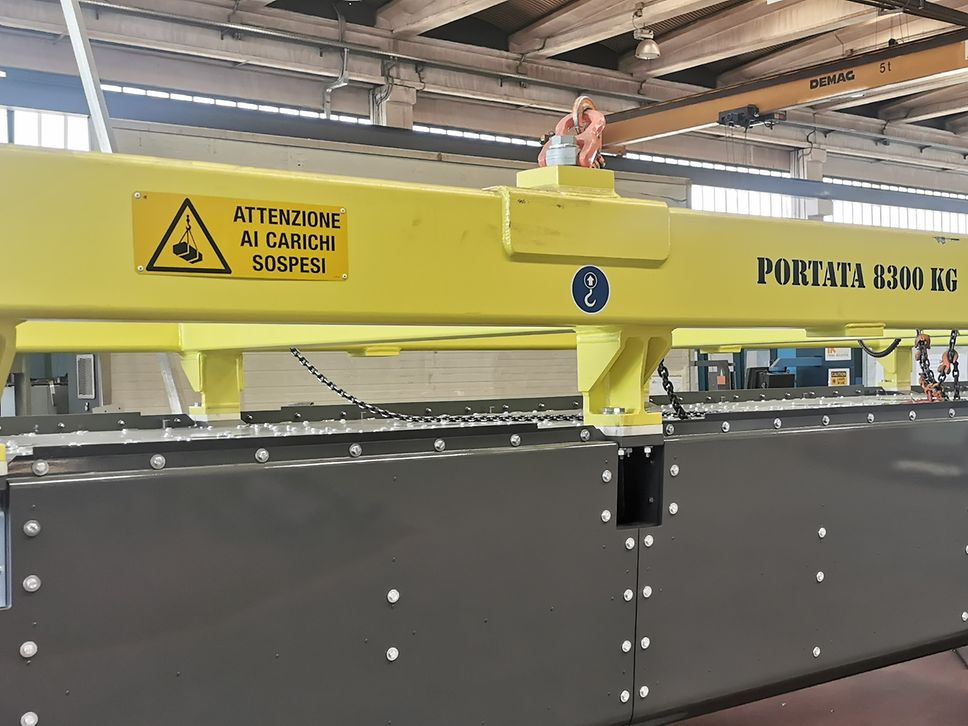
DB ESG, together with the expert support of DB Systemtechnik, initially reviewed and determined the feasibility of Hitachi’s battery concept and considered the best approach to develop this concept further. This initial work was completed in July 2021. Subsequently, Hitachi Rail asked DB ESG to develop this feasibility concept into a fully-fledged design, with detailed manufacturing drawings, enabling the production of three prototypes. On-site support in Italy was provided to Hitachi during the manufacture, installation and testing of these prototype battery rafts.
DB ESG was responsible for managing this project, delivering the design and structural assessment work. DB Systemtechnik specified the high voltage switching technology, and all the project aspects related to fire.
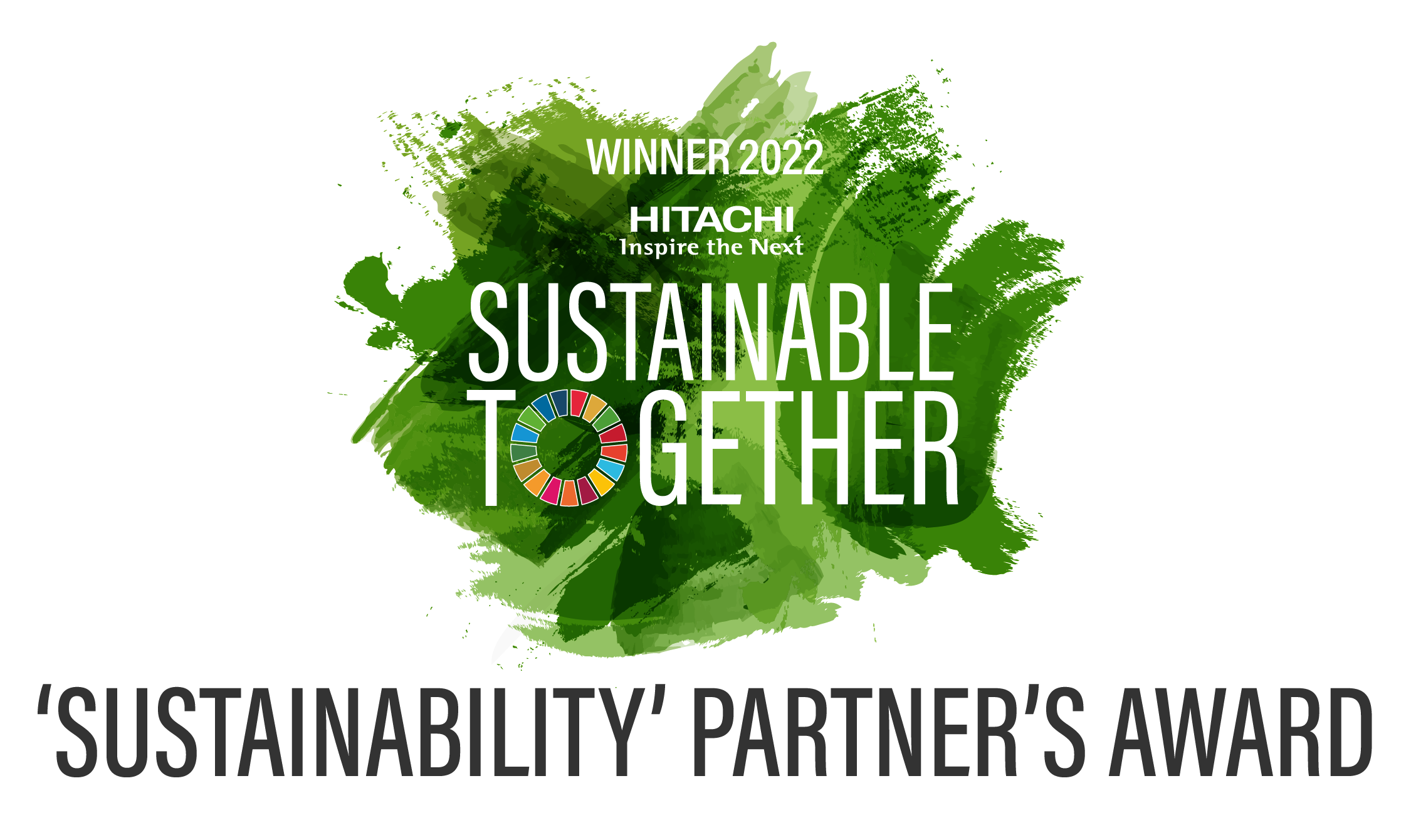
In July 2022, DB ESG, together with Turntide (Battery Unit Supplier), received a ‘Partner Award’ in Sustainability from
Hitachi Rail for this battery systems design project, selected from Hitachi’s global supplier network, which represents thousands of businesses around the world.
Work Undertaken
DB ESG firstly reviewed the safety related functional requirements identified by Hitachi, against the requirements of the known railway standards, producing a summary report outlining any recommended alterations.
Design Concept Development - When developing the concept, DB ESG closely monitored the overall mass and space envelope of the battery raft. This allowed design ideas to be quickly discarded if they caused the battery raft to become significantly over-weight or over-sized. The number of battery units was reduced to 16 during this stage.
DB ESG looked at the following design areas in detail:
Fire barrier – keeping this system safe, whilst ensuring it was compact and lightweight was a significant challenge. This feasibility study focussed on heat insultation and the management of the outgassing, with level feasibility concepts developed.
- Heat insulation – careful consideration was given to the practicality of various options, providing the best balance between space, mass, heat insulation and ease of repair.
- The potential battery raft materials were reviewed to understand how they would cope with the heat generated.
- A review was undertaken into the simulation tools that could be used to verify the design, with regards to fire and battery failure. An investigation was carried out into the physical testing necessary to approve the modelling.
- In the event of a battery failure, smoke and combustion gases would be vented above the roof using pipework routed from the battery raft.
- The fire barrier material fitted to the vehicle raft so that when a battery was removed, the insulation would stay in place.
- The approximate figures for material specification, thickness and mass of the fire barrier were determined. The chosen fire barrier was then modelled as part of the full battery raft concept design.
Battery raft structural assessment - this structure needed to be designed to support the battery units, fire barriers and ancillary equipment, and to protect them on the underframe.
- DB ESG developed the initial SolidEdge design concepts for the battery raft structure based on point loads for the battery units, comparing the merits of the different design options.
- Design concepts were analysed by FEA and the basic block loads for the equipment, using static load cases, were calculated. This provided an indication of the stresses within the structure, helping to determine acceptable materials. The overall mass of each design option was then determined. The FEA assessment enabled the preferred design concept, together with the raft materials to be determined.
- CAD models were produced for the raft variants, providing the space envelope information.
- Final structural validation was completed using FEA of the detailed design and final BU designs.
Battery unit and battery raft interface – each BU needed to be fixed with suitable connectors, that would allow quick connection or removal from the electrical and cooling systems. These interfaces needed to be incorporated into the BU design.
- Electrical components - DB ESG assessed the high voltage DC design and selected suitable high speed circuit breakers, and other HV equipment, to successfully interface with the vehicles’ traction system and the BUs.
- Heating - consideration was given to how to route the water pipes from each BU to the connection point on the vehicle underframe.
- Sensor and fire detection –an independent fire detection system was designed into the battery raft, with sensing elements in each BU pocket and the main raft itself.
- Battery unit outgoings –the pressure at which the gases would be vented was looked at, suitable burst valves were selected, and the route of the venting pipes was designed.
- Battery raft equipment compartment – this compartment sits at the end of the raft, containing the electrical control wiring, HV high speed circuit breakers, and HV fuses for the battery raft. This compartment connected the batteries’ HV, LV and data to the rest of the train. A second compartment at the other end contained the coolant control valves and manifolds. DB sourced the components and DB ESG produced the CAD model of the equipment compartment, and equipment installation design.
A full suite of manufacturing drawings and documentation for the battery enclosure was produced to enable the production of three prototypes.
A fully functional battery enclosure design was developed.
Production of:
- a CAD model of the full battery enclosure.
- a full prototype drawing pack.
- a prototype bill of material.
- an RGS structural compliance report.
- a pressure pulse FEA of battery enclosure outer skin.
- an initial assessment of manufacturability.
Creation of an optimised design suite of drawings.
The first prototype design was optimised for prototypes two and three, looking at mass reduction, whilst keeping the structural integrity, improving the manufacturability and assembly, and ensuring that the battery raft could be effectively maintained.
- Updated CAD model of the full battery enclosure was produced.
- Full production drawing pack.
- Production bill of materials.
- Structural, light-weighting assessment and updated structural compliance report.
Documentation pack containing assembly and maintenance instructions, and a human factor assessment.
Design validation support, including design submission pack for third party assessment.
During the prototype production phase, DB ESG employees were on site in Italy for several weeks to support Hitachi during the manufacture, installation and testing of the prototype battery rafts.